TPE Compounds for Medical Products
Medical products manufactured from PVC containing plasticizers can pose a risk to patients, and children in particular. Plasticizers are not chemically linked with the PVC, which means it is relatively easy for them to leach out of the medical product.
They can migrate into patients’ bodies via outgassing or leaching, for example through infusions or nutrient solutions. Although the corresponding PVC-free medical products are already available on the market, many hospitals continue to use items which contain PVC. These include urinary catheters, blood pressure monitors, IV bags and even endotracheal and feeding tubes.
Various preparations are available for infusion therapy, whereby a distinction can be made between non-specific solutions such as electrolyte solutions (“crystalloids”) or glucose solutions and those with a specific therapeutic purpose, e.g. colloidal solutions for volume therapy, highly-concentrated glucose solutions and other nutrient solutions for nutrition therapy, or buffer solutions for treating acid-base balance disorders.
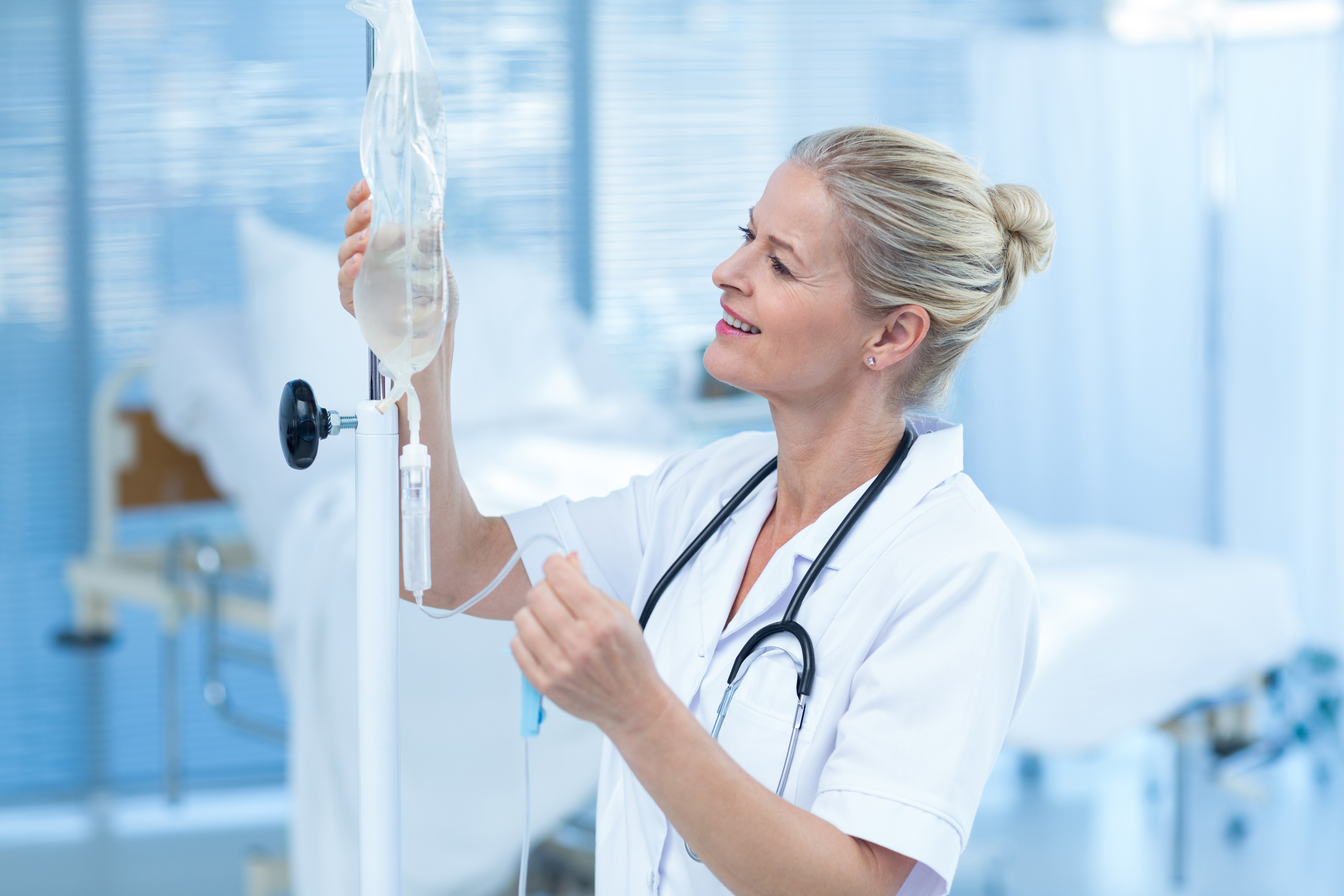
Do you have any questions? Contact us and we will be happy to advise you on your individual requirements.
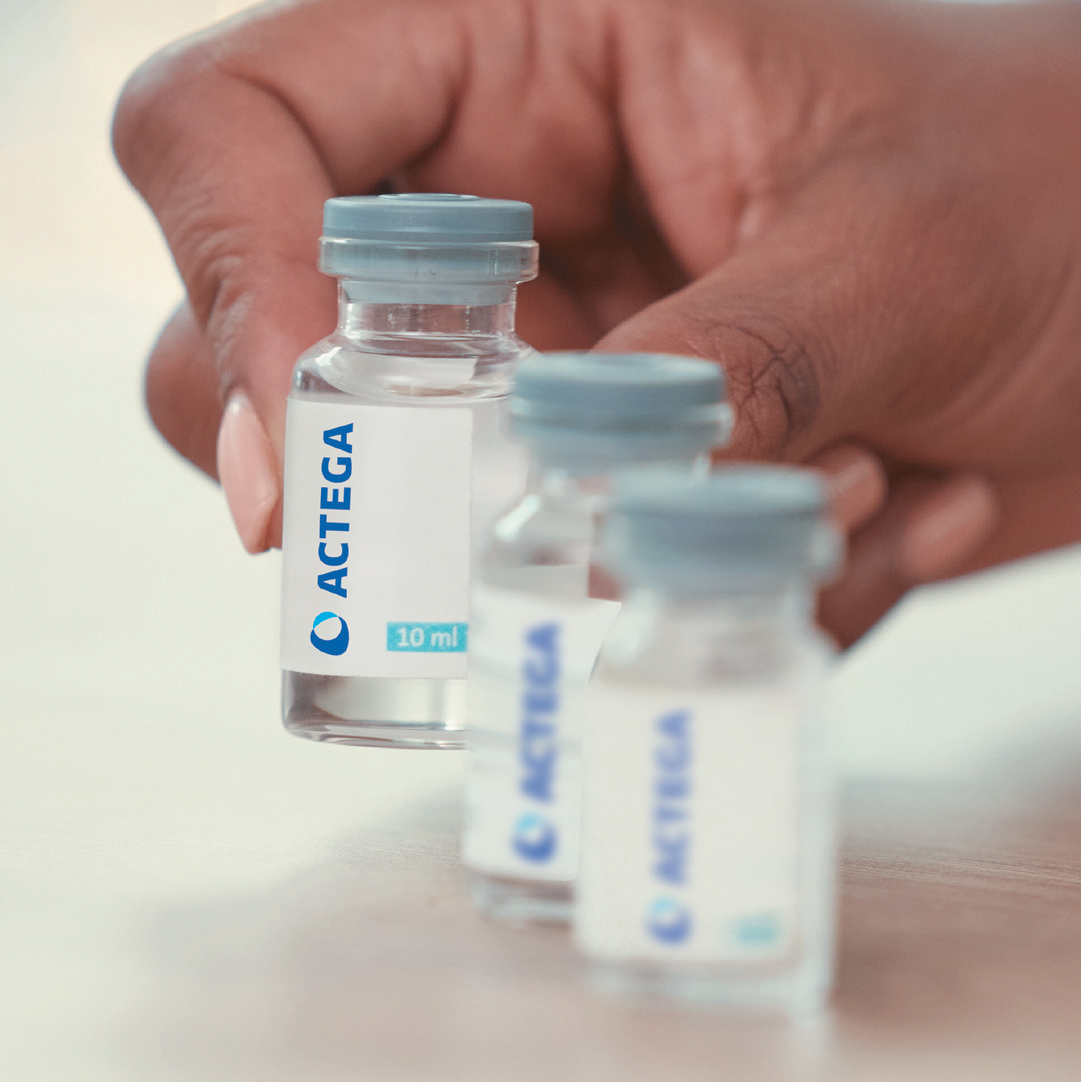
TPE solutions for pharmaceutical stoppers
The TPE compounds specially developed for pharmaceutical stoppers and medical closures enable an economically attractive solution in terms of processing, function and safety. The TPE materials for pharmaceutical stoppers fulfill all the regulatory functions required by USP 381, such as resealability after puncturing with a cannula. Compared to the conventionally used materials, the TPE product solutions for pharmaceutical stoppers are recyclable and convince with easy processability by injection molding and with short cycle times.
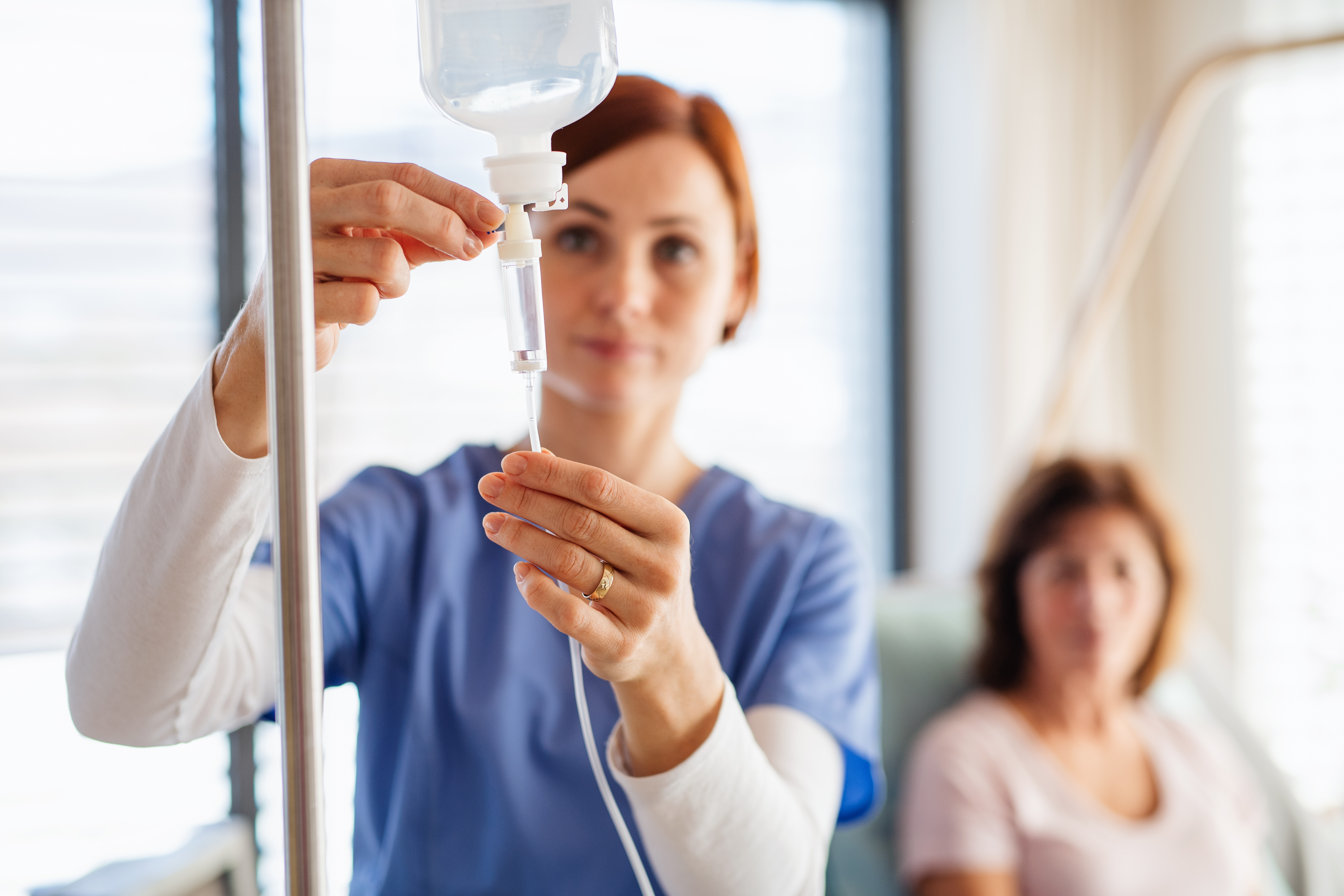
TPE solutions for medical drip chambers
We offer highly-transparent TPEs for drip chambers and tubes in order to guarantee the optical control of the drip process and fluid level. Furthermore, we have optimized our TPEs so that they can be bonded with standard solvents, e.g. the tube with the drip chamber. At the same time, our ProvaMed® TPEs are distinguished by their flexibility, rigidity, and recovery capability. And of course by the fact that they are free of PVC and plasticizers.
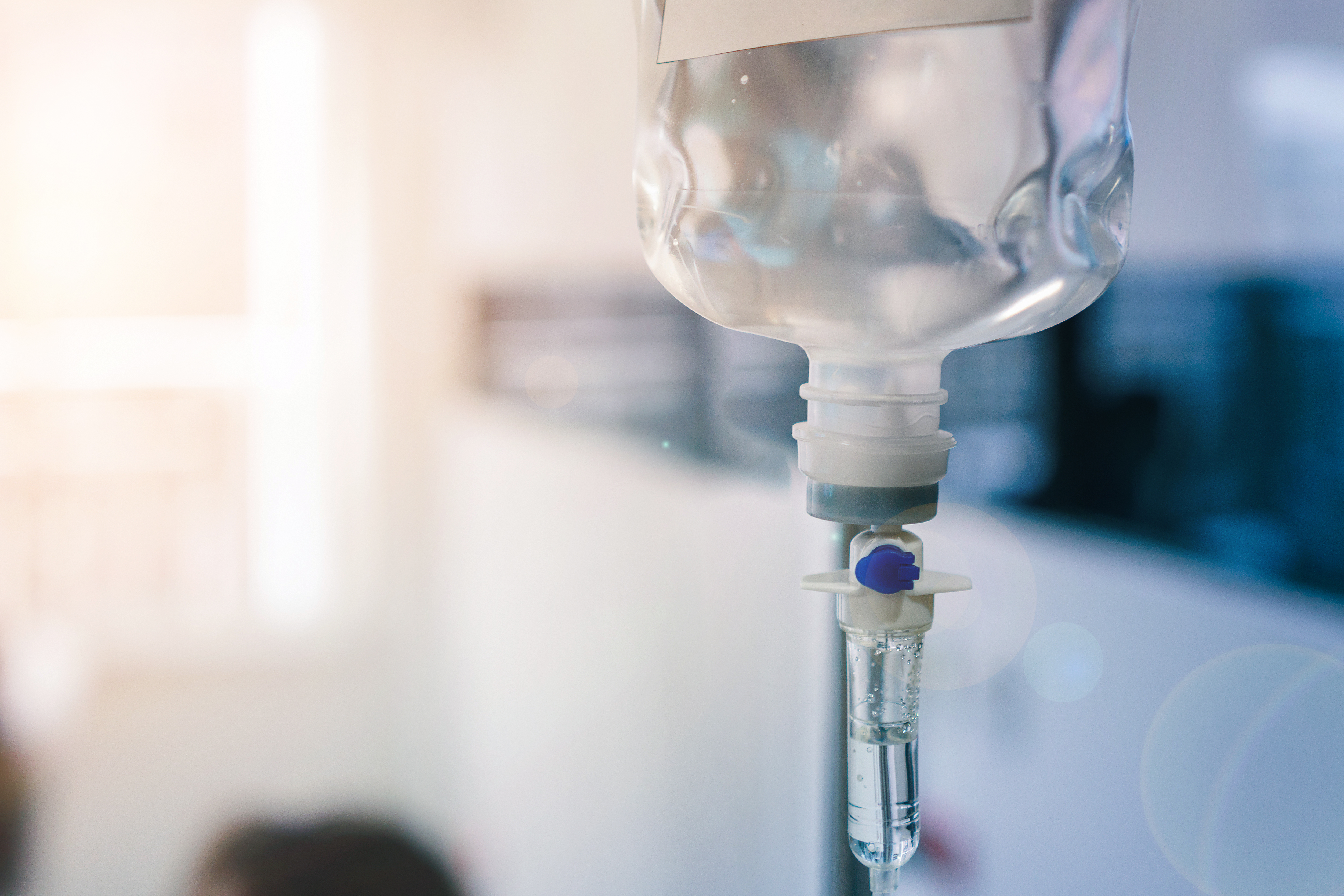
Reclosing intravenous bag closure made from TPE
ProvaMed TPE for IV are particularly efficient and hygienic in terms of processing. The material only comprises raw materials which meet the specifications of the medical market in order to eliminate the possibility of contamination. Because TPE materials are so highly elastic, the septum reliably seals off the intravenous bag when the drip tube is removed. The actual production process is medically safe.
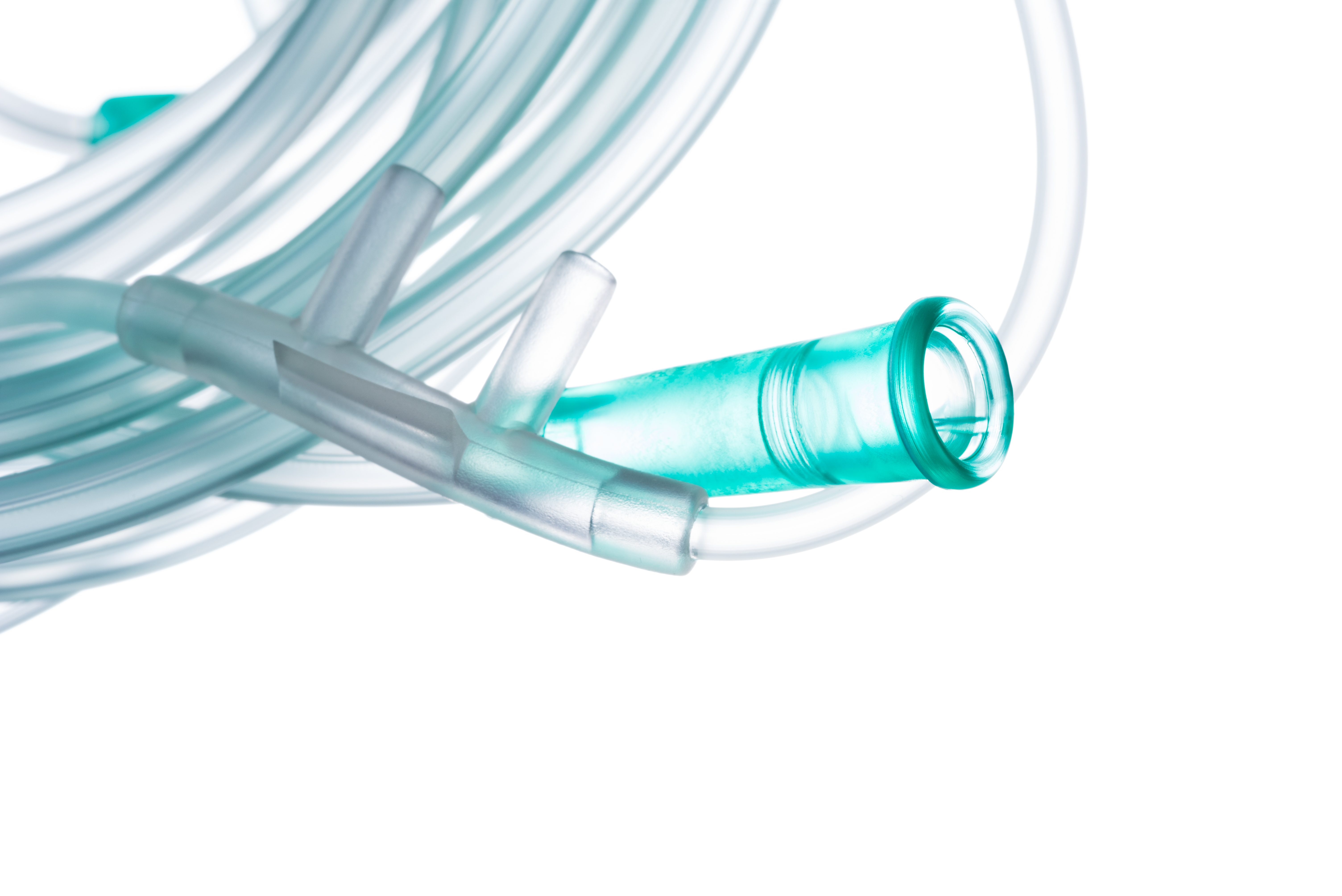
TPE for medical and pharmaceutical tubes
ACTEGA specializes in customer-specific developments with a wide range of functional options for medical and pharmaceutical tubing. In addition to the possibility of customized TPE compounds, we offer a portfolio of outstanding TPE extrusion types for tube production under the ProvaMed brand.
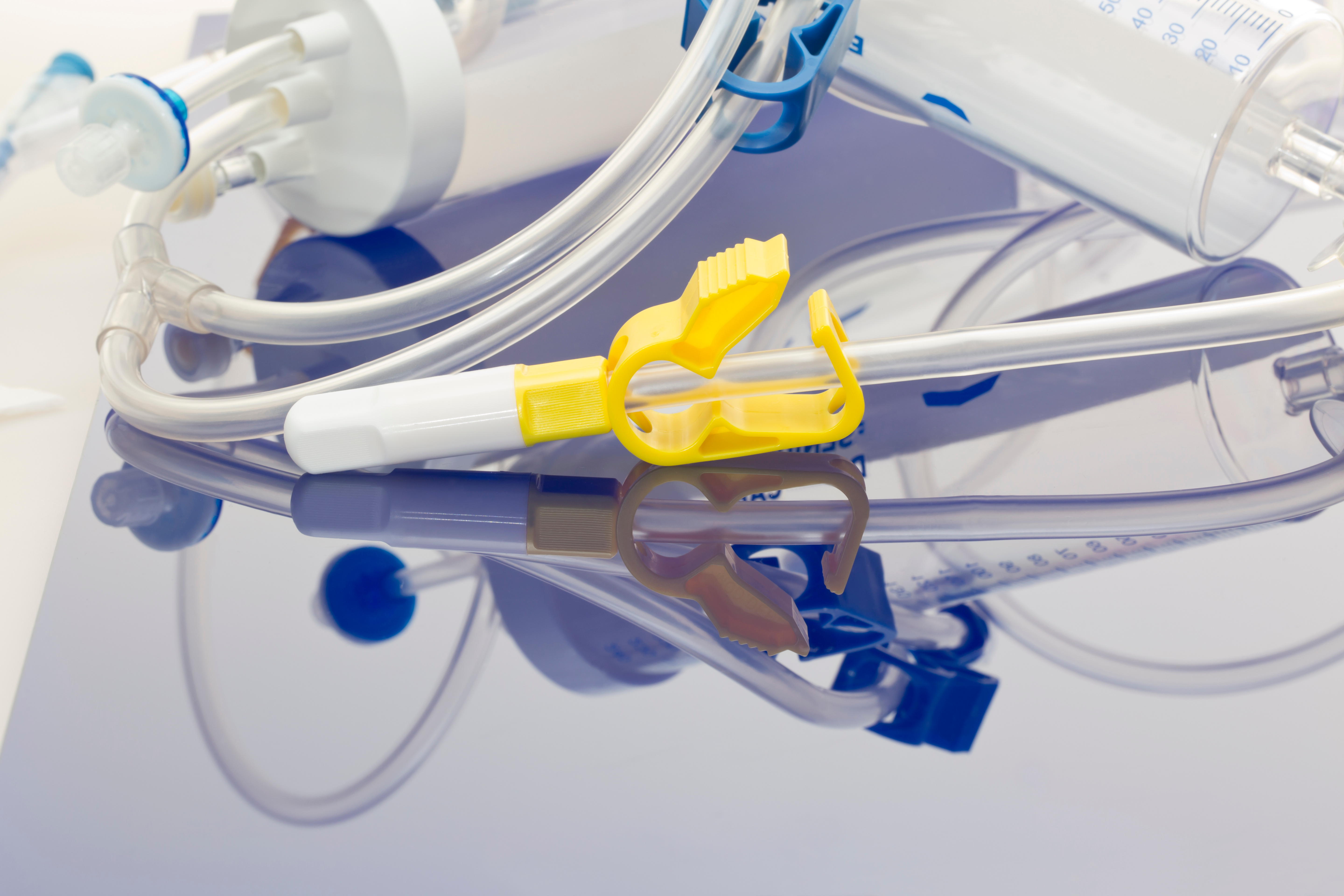
TPE solutions for two- / multi-component injection-molding
As a general rule, our TPEs can be processed in economical two-/multi-component injection-molding as the products display perfect adhesion to polystyrene and ABS. For example, multi-component hard/soft compounds are possible in applications comprising TPEs and ABS, PC or PP. Such adhesion-optimized TPEs enable you to achieve shorter cycle times while reducing the efforts associated with assembly.
Free from PVC and phthalate plasticizers
As in many areas of medical technology, most plastic-based tracheal cannulas have been manufactured from PVC to date. But here, too, a rethink has taken place. ProvaMed® TPE meet the demand for freedom from PVC and plasticizers containing phthalates. They can be processed very well on all common injection-molding and extrusion machines. The flow properties of the material can be precisely adjusted for processing in extrusion. In multi-component injection-molding, tracheal cannulae and cannula shields can be produced in a single economically-favorable step and the adhesive properties of the TPE can be designed and optimized for the material of the connector.
An excellent solution – confirmed by extensive testing – was also found for the aspect of solvent bonding. This is because it is often necessary for microtubes to pass through the cannula shield and be bonded to the outer sheath using common solvents. These bonded joints must also survive the sterilization required after manufacture and printing. Even after gamma sterilization of ProvaMed® TPEs with 50 kGy, no impairment of the material properties can be detected.
Our brands for medical TPE
ProvaMed®
Portfolio of standard products for medical technology and for customized TPEs for highly-sensitive areas of application.